What is Lean manufacturing?
Lean manufacturing means a manufacturing system that eliminates what is not profitable for the business. Thus, the key point in lean production is how to detect what is not profitable and eliminate it.
This is done by empowering each individual so that they can feel able to take their own, full stand and make the greatest possible contribution. Because above all, manufacturing employees will understand the product and their work area best. When it comes to lean manufacturing, we often think of “eliminating waste”. However, the highest goal of Lean is to determine value based on the customer’s perspective, thereby continuously improving to bring perfect value to customers through a waste-free value creation process. fee.
What’s the point of eliminating waste if you can’t create more valuable products for customers, right?
Here’s a 5-step plan to put you on the road to lean success.
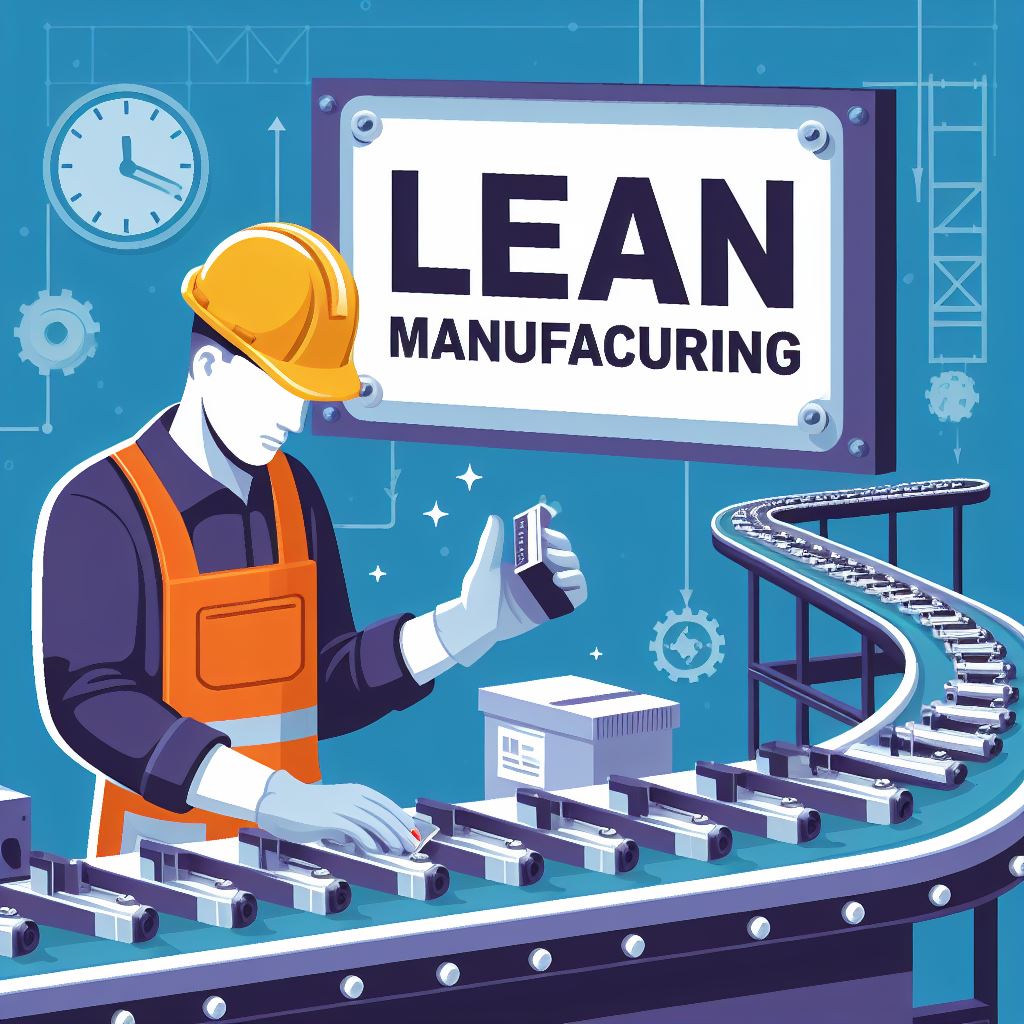
5 steps to get started with Lean manufacturing
Step 1: Go Lean For The Right Reasons
Some companies view lean manufacturing as a necessary evil – one they must somehow fake their way through in order to impress customers. Big mistake. Today’s customers are savvy and can quickly see through this facade.
A successful lean production implementation depends on a commitment to make continual, lasting improvements in your manufacturing processes.
The driving force behind adopting lean principles should be an objective to create value through eliminating waste.
The right philosophical approach will set the foundation for success.
Step 2: Get Everybody To Buy In
Bringing change to an organization takes time – even when times are good.
The adoption of lean principles means instilling a mindset of continuous improvement throughout your company and continually seeking ways to improve work flow and value output.
This new culture requires everyone in your organization to be engaged in the process and be kept abreast of the progress.
To encourage participation, set up a clear channel of communications to share productivity gains so you can build momentum and support.
Step 3: Devise An Implementation Plan
An important step when implementing a lean strategy is to establish a plan of action.
Start by identifying the obvious areas you need to address. Do you have delivery issues? Problems with lead times? Maybe your downtime has increased?
Your plan – complete with attainable targets – will allow you to show those in upper management and those on the shop floor how you are progressing and reaching your milestones as planned so you can continue to garner support.
Having a plan is essential for keeping you and your team on track for increased productivity.
Step 4: Just do it!
Don’t overthink your decision to start implementing lean manufacturing principles.
After careful planning, start small by directing your efforts at one product line so you can demonstrate proof of concept prior to a broad-scale rollout.
The best way to get lean is to act that way. Get started so you can build on your efforts and results.
Create a follow up system that will allow you to evaluate the changes you made to ensure you’re moving forward and not falling back into old habits.
Step 5: Be Sure To Have Lean Tools to Accurately Measure Your Results
One sure way to accurately measure Overall Equipment Effectiveness (OEE) is to implement a system for measuring your lean production management.
All too often, companies make manufacturing quality improvements that only fix the symptoms of inefficient production methods rather than the root cause.
Create a “visual” shop with displays and controls used throughout your manufacturing plant that makes the state and condition of manufacturing processes easily accessible and clear to everyone. Lean manufacturing tools such as machine monitoring software give you accurate data on downtime and slow cycles that you can use to make practical decisions.
Today’s competitive global environment demands lean efficiency.
Not only will you will benefit from a business culture focused on mutual problem solving, this type of an environment empowers and encourages all team members to contribute to quality operations which results in the optimum customer value needed for competitive advantage in the modern marketplace.
Contact us now at!
DATA INSIGHT TECHNOLOGY VIETNAM COMPANY LIMITED
- Hotline: 0916.848.638
- Hanoi office: Số 6 Kim Đồng, phường Giáp Bát, Quận Hoàng Mai, Thành phố Hà Nội, Việt Nam
- HCM City office: 99 đường Cộng Hòa, Phường 4, Tân Bình, Thành phố Hồ Chí Minh, Việt Nam