In manufacturing, OEE stands for Overall Equipment Effectiveness. OEE serves as a widely recognized standard and reference for a plant’s productivity in the industrial sector. Measuring OEE is considered an evaluation method by manufacturers to understand and identify potential losses during production, while also using it as a historical benchmark to measure and improve OEE over time.
This article aims to provide a clear understanding of OEE and methods to enhance productivity in manufacturing, whether you are using OEE software for automated data collection and calculation, employing manual methods, or are new to OEE metrics. General Lean methods for boosting OEE and specific strategies for improving productivity will be elucidated.
What is OEE?
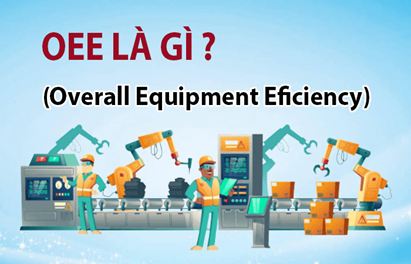
OEE—Overall Equipment Effectiveness—is a metric measuring the productivity of equipment, divided into three main components: Availability, Performance, and Quality.
OEE is considered one of the most important metrics in manufacturing (at least for productivity). Measuring OEE is crucial for manufacturers as it provides them with a Key Performance Indicator (KPI) to better understand the actual operational efficiency and productivity of a plant.
So, what does measuring this entail?
Measuring OEE helps manufacturers understand the percentage of actual operating time during which a plant was truly productive and efficient. It defines “actual operational time” as the time a plant produces as many high-quality parts as possible within a specified timeframe.
For example, a plant with a high OEE ratio efficiently utilizes operating time to produce more high-quality parts within the same timeframe compared to a plant with a low OEE ratio. Therefore, measuring and improving OEE is essential for enhancing productivity and efficiency in manufacturing.
Calculating OEE
OEE Formula
- Availability (A): Tracks the frequency and duration of machine downtime, whether planned or unplanned. Ideally, manufacturers should encounter no downtime to achieve 100% results. Some formulas calculate only effective working time and full operating time to better evaluate performance without disrupting results with planned downtime.
- Performance (P): Measures production speed and examines any time-wasting activities. Performance is often evaluated by comparing ideal cycle time with actual cycle time.
- Quality (Q): Represents the percentage of produced parts meeting or exceeding quality standards.
How to achieve a safe OEE level for each plant?
Each of these three factors is evaluated on a scale from 0 – 100%. Achieving 100% is an ideal goal for manufacturers; however, reality differs. To be considered world-class, manufacturers only need to achieve an 85% OEE, and of course, achieving this figure is not easy. On average, plants have an OEE of around 60%.
There are two formulas for calculating OEE:
- OEE = (Number of good units produced x Cycle time) / Planned production time
- OEE = Availability (A) x Performance (P) x Quality (Q)
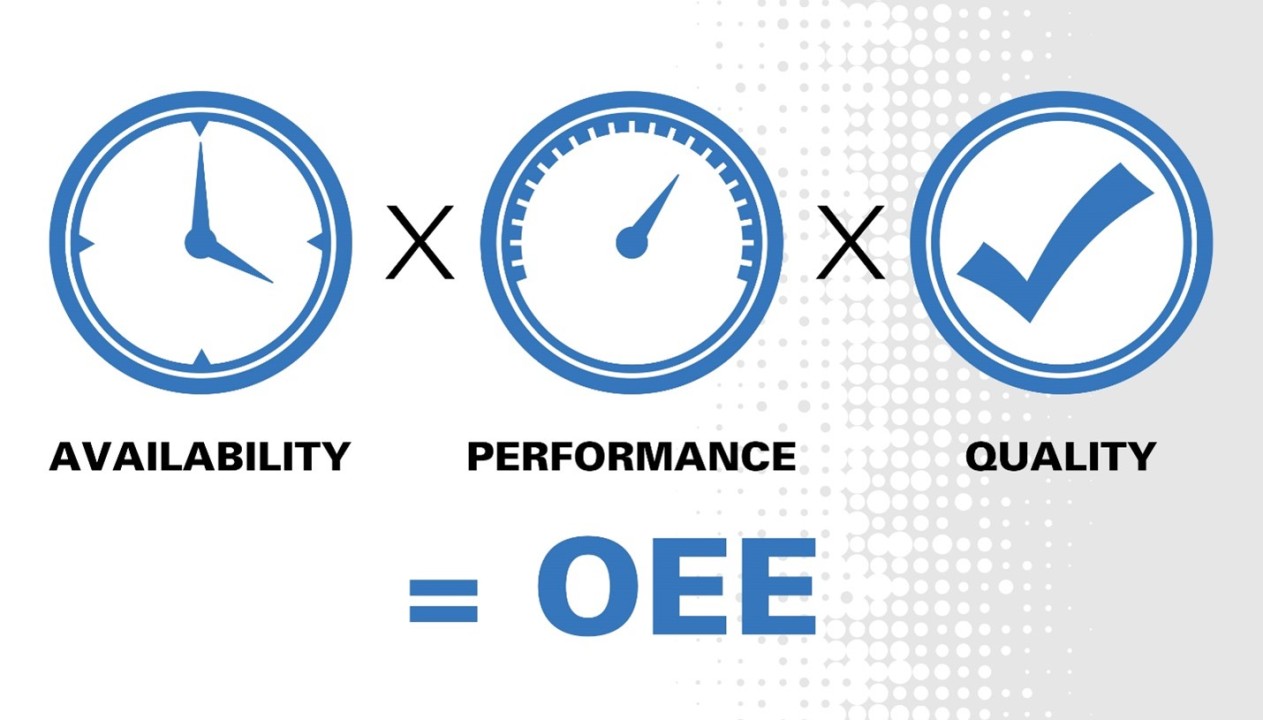
The combination of these three factors helps manufacturers understand the challenges they face and where waste occurs. Thus, manufacturers can see if their machines are operating efficiently or not.
Example:
Day 1 | Day 2 | Day 3 | |
A | 80% | 70% | 75% |
P | 90% | 75% | 85% |
Q | 85% | 85% | 80% |
OEE | 61.20% | 44.63% | 51.00% |
Strategies to Improve OEE (Overall Equipment Effectiveness)
Six sigma
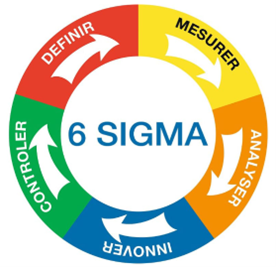
Six Sigma is a method focused on improving the fundamental processes of manufacturing operations. The primary way it achieves this, according to Six Sigma principles, is by minimizing variability, meaning executing business processes effectively, efficiently, and consistently in every operation possible. For Six Sigma, reducing variability in production processes is crucial because variability leads to instability and difficulties in predicting outcomes.
In addition to minimizing variability, Six Sigma also concentrates on reducing or eliminating product defects. This is crucial because product defects not only reduce quality but also increase repair costs and downtime. By focusing on reducing variability and defects, Six Sigma helps increase the stability and efficiency of production processes, thereby enhancing the effectiveness and reliability of the final product.
Lean manufacturing
This is where OEE was born. Lean Manufacturing focuses on maximizing resource utilization to eliminate waste and allows manufacturers to do more with less. Familiar concepts related to Lean Manufacturing include value stream mapping and Kaizen, which means continuous improvement.
Theory of Constraints (TOC) is a management philosophy in manufacturing that views a system’s performance as being limited by its weakest link. TOC identifies the constraints limiting development, growth, and performance, such as the weakest link in the system. Users are guided to identify and exploit these constraints, change other organizational processes, and ultimately reduce constraints. Constraints often include people, policies, and equipment.
Seven Strategies to Improve OEE Across the Entire Plant
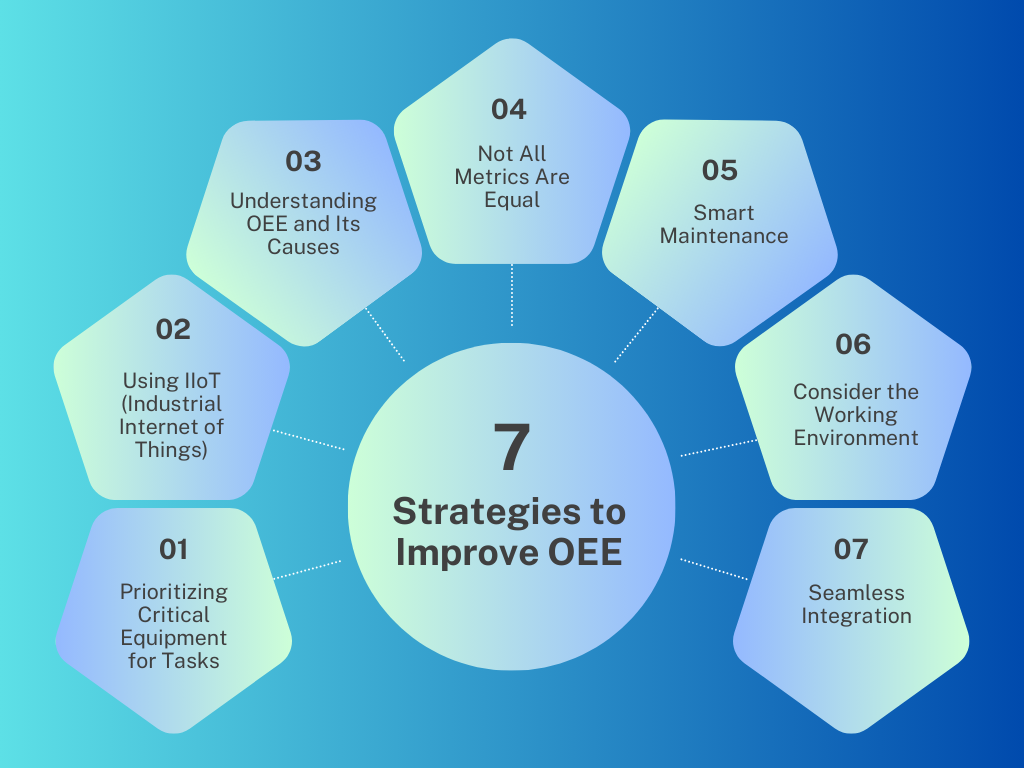
Here are some useful strategies that manufacturers can apply to improve OEE. Each strategy provides a different approach to better understand how to use your equipment and identify your major sources of waste. Improving OEE can be addressed in various ways: identifying bottlenecks in the production process, developing better work processes, improving maintenance systems, reducing machine downtime, etc.
Prioritizing Critical Equipment for Tasks
The strategy of prioritizing critical equipment for tasks focuses on optimizing the efficiency of the most important equipment and assets in the production process. When these equipment fail or malfunction, the consequences spread to other production steps, significantly affecting the system’s performance and productivity.
Improving OEE for these assets will bring significant benefits and can positively impact the entire value chain of the business. Therefore, to achieve this, manufacturers need to focus on investing and caring specifically for these critical machines and assets through cost-effective maintenance programs. This ensures that the equipment can operate continuously and reliably, enhancing productivity and achieving the business’s production goals.
Using IIoT (Industrial Internet of Things)
Connecting manufacturing devices and smart factories, using connected devices to collect and analyze real-time data. When everything is “Internet-enabled,” operators can access devices in their factories anytime, using just a smartphone with an Internet connection. These devices provide instant information about OEE, and the collected data can be combined and analyzed to help managers gain deeper insights and make the best decisions, enhancing OEE in the future.
Understanding OEE and Its Causes
When hearing about OEE solutions, although initially seeming straightforward, they are actually complex and nuanced. Typically, OEE-related issues stem from earlier problems that are only detected in later production stages. This could be related to purchasing processes affecting supplier quality, thereby impacting machine performance and other production processes.
To understand the causes of the OEE index, one needs to understand its constituent factors and how they interact. By studying the “gears” of OEE, you can identify the fundamental factors causing issues and affecting the performance of the production system. For example, issues in the procurement process could lead to suppliers delivering poor-quality components, thereby reducing machine performance during production.
Not All Metrics Are Equal
What makes a significant difference in one business may not hold much value in another. It’s important to adjust OEE formulas according to your manufacturing business; otherwise, inaccurate results (and misdirected optimizations) will lead to unexpected outcomes where and when needed.
Smart Maintenance
Ensuring machines can operate during expected production times is a crucial component of OEE (availability). This is why a smart, automated maintenance program is necessary, helping manufacturers pinpoint maintenance intervals, prevent unnecessary and costly downtime, avoiding unnecessary downtime during maintenance without proper preparation.
Consider the Working Environment
How do surrounding conditions affect machine performance? Excess waste, oil, smoke, vibrations, dust, and even poor lighting can affect the OEE of equipment, as well as factors that may be characteristic of factory workers. If you can’t clearly see what you’re doing, you may move slower than if you could see clearly.
Seamless Integration
Connecting systems to have seamless information flow is crucial to enhancing OEE. When manufacturers monitor their machines and operations to automatically collect data, they can integrate with other systems to develop efficiency.
There are countless use cases created through integrating various systems. The most crucial part is having a data-driven foundation with up-to-date production data; machines and operators operating on the factory floor.
Data Insight is scalable as it collects this production data in real-time and can provide information to other systems for analysis and automation. Thus, other management systems like CMMS, MES Lite can leverage accurate and real-time production data to enhance productivity.
For example, a machine condition reaching a predefined threshold could trigger a work order in CMMS and automatically notify a maintenance team member.
Using Data Insight Solutions to Monitor and Improve OEE
For us, production data is always readily available for immediate decision-making, historical data analysis, or automation triggers. Accurate, contextualized data can help you assess OEE metrics and measure improvements based on any process changes you’ve implemented. With our plug-and-play solution, Data Insight provides OEE reports instantly so you can see immediately on the Availability, Performance, and Quality aspects.
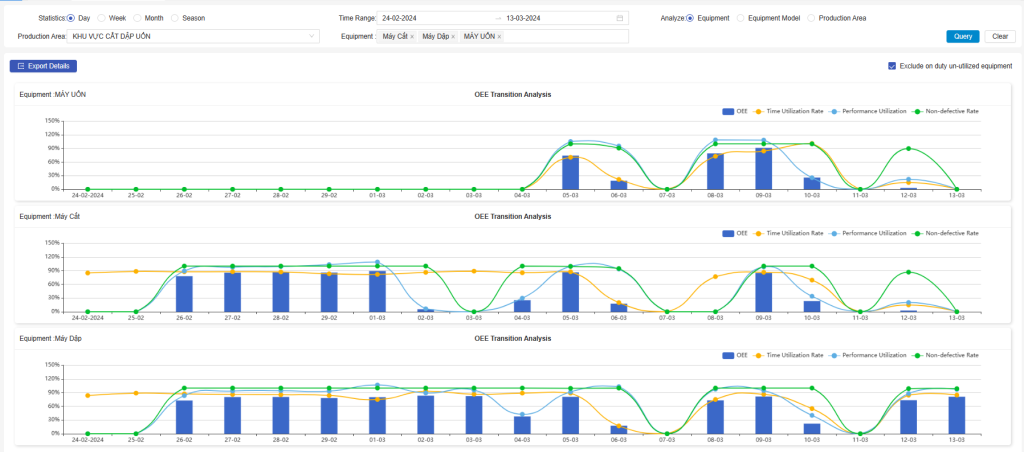
Production data is aggregated for easy monitoring of OEE indices across your plant, or you can track detailed information about specific equipment or production areas.
In addition to direct monitoring through our software, you can also export data to Excel files and create customized reports as needed.
If you’re interested in how Data Insight can help you monitor and improve OEE, don’t hesitate to schedule a demo with our team.
Contact us now at!
DATA INSIGHT TECHNOLOGY VIETNAM COMPANY LIMITED
- Hotline: 0916.848.638
- Hanoi office: Số 6 Kim Đồng, phường Giáp Bát, Quận Hoàng Mai, Thành phố Hà Nội, Việt Nam
- HCM City office: 99 đường Cộng Hòa, Phường 4, Tân Bình, Thành phố Hồ Chí Minh, Việt Nam