Manufacturing operations can no longer rely solely on manual interventions and archaic tracking methods. In today’s data-driven world, software solutions have emerged as a vital tool for factory optimization. This blog will dive deep into the nuances of OEE software, its benefits, and why it’s a must-have for modern manufacturing units.
What is Software for OEE?
OEE stands for Overall Equipment Effectiveness. It’s a benchmarking metric that evaluates how efficiently a manufacturing operation is utilized, factoring in three primary components:
- Availability
- Performance
- Quality
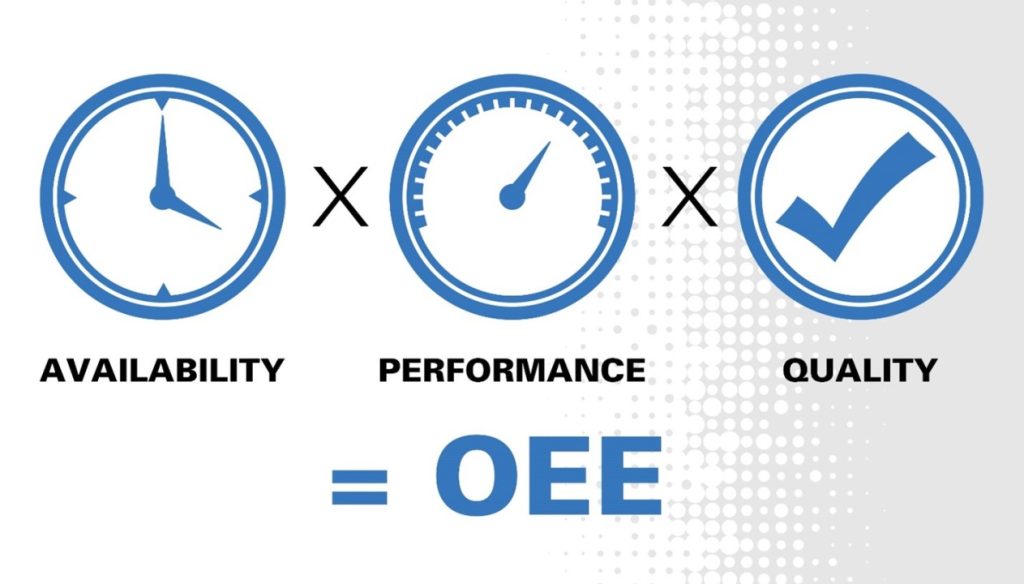
Data Insight uses real-time production data sourced directly from machine controls, automatically generating OEE reports, a much-needed upgrade from manual methods.
How Does it Work?
Real-time software solutions for OEE measure variables related to performance, availability, and quality by directly connecting to machines. The software automates OEE data collection, whether through an OEM-embedded capability or analog/Ethernet connections using edge devices and sensors.
Once collected, the data undergoes a cleansing and standardizing process. Advanced analytics platforms then convert this raw data into actionable insights, assisting managers and operators in decision-making.
What is a Good OEE Score?
- An OEE score of 100% is perfect production; this requires only manufacturing good parts as fast as possible, with no unplanned downtime.
- An OEE score of 85% is considered world-class for manufacturers. For many companies, it is a legitimate and reasonable long-term goal.
- An OEE score of 60% is relatively typical for manufacturers but indicates room for improvement.
- An OEE score of 40% is standard for manufacturing companies just starting to monitor and improve their manufacturing performance.
In most cases, OEE can be easily improved by monitoring your machines and learning where the inefficiencies lie within the manufacturing process.
Modern manufacturers are adept at swiftly identifying and addressing problems. However, the real challenge lies in solving the immediate problem and understanding its root causes. When calculated and optimized accurately, OEE provides insights into both the macro and micro aspects of these problems. And it is here that high-quality OEE solution becomes invaluable.
The Importance of Automated Machine Monitoring
Enhancing OEE commences with integrating a machine monitoring system into your shop floor. This system should be able to autonomously deploy OEE data collection, sourcing data from both machines and operators. Such a system ensures heightened production visibility, essential for OEE improvement.
Data Insight’ standout software solution for OEE equips manufacturers with a cutting-edge tool to automate OEE data collection. But its utility isn’t confined to merely deciphering the present OEE. This software plays a pivotal role in pinpointing potential challenges and discerning areas of inefficiency. The questions it helps answer are many: Is the bottleneck in performance, quality, or availability? Can specific machines, jobs, shifts, or processes be identified as the culprits?
OEE: Not Just a Metric, but a Continuous Improvement Catalyst
Merely regarding OEE as a statistical performance figure undermines its profound impact. It stands as the bedrock of a sustainable continuous improvement strategy. Visionaries in the manufacturing domain harness OEE systems to proactively discern issues and foster a culture of accountability within the shop floor environment.
When used to its full potential, understanding and leveraging OEE aligns managerial objectives with real-time operations at the plant level. This alignment, in turn, motivates all staff members to adopt a proactive stance. As everyone collaborates and aligns, the outcome is unmistakable: surging productivity and burgeoning revenues.
Selecting the Ideal OEE Solution
- Set clear goals
Identify your objective before diving into the vast sea of options. Are you looking to automate data collection, diagnose existing issues, or drive manufacturing enhancements? A well-defined goal will streamline the software selection process.
- Identify data types
OEE software can capture a range of data and offers varied analytical capabilities. Familiarizing yourself with the data you wish to monitor is crucial.
- Prioritize real-time analysis
Automated data collection combined with real-time analysis maximizes OEE improvement efforts. Systems that integrate high-frequency data from embedded and attached devices, streaming it to cloud platforms, will refine the entire manufacturing operation’s data analysis.
- Customize for end-users
Having analyzed data is only part of the equation. Delivering it to the correct individuals in a comprehensible format ensures timely action.
- Put data into action
Harness the power of real-time insights. Software for OEE identifies data trends that can be the foundation for root cause analyses, innovative maintenance strategies, and cost reductions.
Essential Features
A robust OEE solution should:
- Facilitate automated data collection
- Offer customizable reporting tools
- Enable automated quality monitoring
- Provide real-time alerts and notifications
- Allow benchmarking capabilities
- Present intuitive real-time OEE dashboards
The Impact of Software for OEE on Manufacturing
Automating OEE data collection with software like Data Insight can transform operations. While manual methods can be riddled with inaccuracies and biases, an OEE solution offers visualization, precise reporting, and real-time prescribed actions. Savvy customers know that the more a modern manufacturer embraces new smart manufacturing and IIoT technologies, the more likely their jobs will be finished on time.
Such laser-focused problem detection and analysis empower managers and operators to establish optimized maintenance programs, enhance production quality, and implement continuous improvement initiatives.
When is the Right Time to Adopt Software for OEE?
If the manufacturing buzz around software for OEE is resonating louder, there’s a rationale behind it. From small-scale manufacturers to industry giants, the shift towards automated machine monitoring is evident.
Consider integrating OEE software solutions into your operations if:
- Your customers demand OEE tracking.
- Deliveries aren’t meeting deadlines.
- You overestimate your uptime.
- You’re aiming to enhance company culture.
- Financial losses due to inefficiencies are becoming evident.
Implementing an OEE Software System: A Step-by-Step Guide
- Begin with understanding your existing OEE. While it might be manual and tedious, it offers a benchmark.
- Determine the primary purpose behind adopting the OEE system.
- Not all OEE solutions cater to every industry. Tools like Data Insight cater to a diverse range of OEMs and machine ages.
- Familiarize your team with the system without overwhelming them.
- Consider a full-scale implementation, as the real-time data reflects actionable insights.
Why Choose OEE Software?
In a world where precision, efficiency, and continuous improvement are the hallmarks of successful manufacturing, embracing tools becomes advantageous and essential. As this guide has covered, OEE isn’t just another metric; it’s a compass pointing manufacturers toward their pain points, inefficiencies, and growth opportunities.
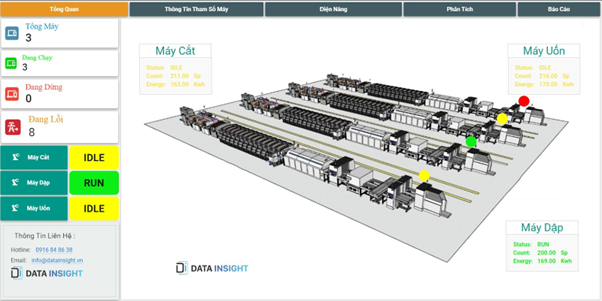
Data Insight embodies this evolution, offering solutions that can redefine how manufacturing floors operate. By automating data collection, refining processes based on real-time insights, and fostering a culture of proactive problem-solving, OEE software solutions set the stage for a new era of manufacturing excellence.
As industry challenges evolve, so should our approaches – and embracing robust OEE software is a definitive step in the right direction. Interested in transforming your manufacturing operations with Data Insight? Get in touch to explore our state-of-the-art OEE tracking software solution.
If you’re interested in how Data Insight provide you our OEE software, improve efficiency of your plant and drive profit for your business, don’t hesitate to schedule a demo with our team.
Contact us now at!
DATA INSIGHT TECHNOLOGY VIETNAM COMPANY LIMITED
- Hotline: 0916.848.638
- Hanoi office: Số 6 Kim Đồng, phường Giáp Bát, Quận Hoàng Mai, Thành phố Hà Nội, Việt Nam
- HCM City office: 99 đường Cộng Hòa, Phường 4, Tân Bình, Thành phố Hồ Chí Minh, Việt Nam