OEE’s role in manufaturing
The Overall Equipment Effectiveness (OEE) plays a crucial role in enhancing manufacturing efficiency. OEE is a method used to measure and monitor the overall performance of production equipment and processes. By applying OEE calculations, you can identify causes of time or resource waste during production and improve efficiency to increase the speed and production of manufacturing systems.
OEE calculations help accurately pinpoint waste caused by the 6 Big Losses. These are disruptions that undermine lean manufacturing goals.
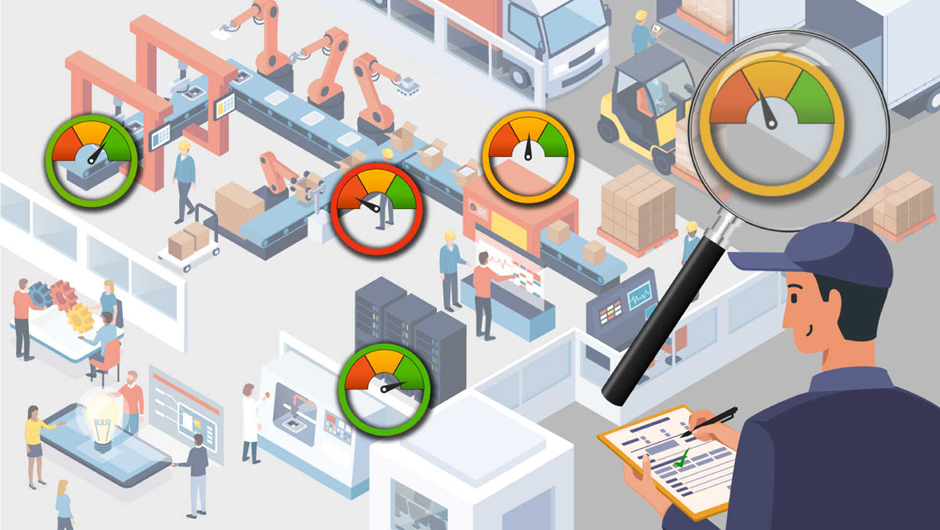
The 6 Big Losses
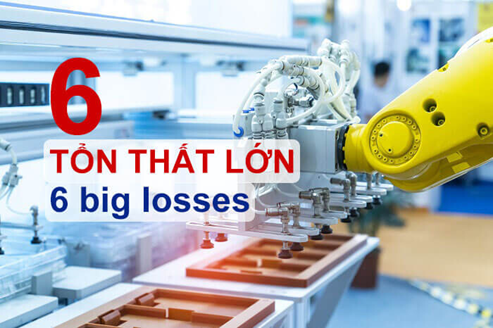
- Equipment breakdowns: Unexpected machine or equipment failures that lead to downtime and production disruptions.
- Setup and adjustments: Time and effort required to set up machines and make adjustments for production, leading to time waste.
- Small stops during equipment operation: Short machine stops due to minor issues, often under 5 minutes, which typically do not require technical maintenance presence.
- Equipment operating at reduced speeds: Production speeds lower than maximum capacity that decrease overall equipment effectiveness (OEE).
- Startup rejects: Products discarded during machine startup after setup, causing production delays and material waste.
- Production rejects: Products that do not meet standards and are discarded after production, resulting in material and time waste.
By identifying and minimizing losses from these causes, businesses can improve the overall performance of their manufacturing processes and achieve lean manufacturing goals.
To calculate OEE
1. The standard formula: OEE = % Availability x % Performance x % Quality.
- % Availability (A): The ratio of time equipment is available for production compared to scheduled operating time.
- % Performance (P): The ratio of actual output to the maximum output the equipment can produce.
- % Quality (Q): The ratio of good output to total output.
2. The Throughput Ratio method is useful for assessing an overall process or production line.
– OEE = (Number of good products x Cycle time) / Planned production time.
An example of an assumed OEE calculation
Suppose an ice cube tray factory applies the Japanese Kaizen method—a philosophy of lean production and continuous improvement.
Before Kaizen implementation, every 1,000 ice cube trays produced resulted in 75-95 defective trays.
Under Kaizen, employees focus on continuously improving the production process. They use OEE calculations to assess each step in the ice cube tray production process to identify areas for improvement.
In this example, a timing issue was identified in one step of the process where a machine would reset for an extra three minutes while ice cube trays continued moving through the line.
As a result, every 90 minutes, a batch of ice cube trays was molded incorrectly.
Using OEE calculations, the company decided to slow down the manufacturing line for those 3 minutes. This adjustment increased the quality rate and reduced waste.
Although there is no universally agreed-upon ideal OEE target, a score of 85%, using the standard formula above, indicates superior performance.
The key is not to focus solely on the actual number but to continuously seek ways to improve efficiency of manufacturing operations.
Are you ready to learn how monitoring equipment can improve your OEE and your profitability?
If you’re interested in how Data Insight can help you monitor OEE, improve efficiency of your plant and drive profit for your business, don’t hesitate to schedule a demo with our team.
Contact us now at!
DATA INSIGHT TECHNOLOGY VIETNAM COMPANY LIMITED
- Hotline: 0916.848.638
- Hanoi office: Số 6 Kim Đồng, phường Giáp Bát, Quận Hoàng Mai, Thành phố Hà Nội, Việt Nam
- HCM City office: 99 đường Cộng Hòa, Phường 4, Tân Bình, Thành phố Hồ Chí Minh, Việt Nam