In industries that demand high precision, enhancing the productivity of production equipment is crucial to meeting standards and desired output levels. To monitor and improve the machine productivity on the production line, directly collecting data from equipment is the most effective approach. Let’s review important metrics such as production quantity, cycle time, production costs, and downtime to measure and adjust production operations. These are fundamental steps to optimizing workshop operations and ensuring stable production according to standards.
What is Machine Productivity?
Machine productivity is the ratio of output to input, measuring the rate of output and the readiness to meet customer demand.
The outputs are finished products or goods produced by manufacturers. Machine productivity measures the ability of a machine to utilize input factors such as raw materials, labor, and produce finished goods or products.
It’s important not to confuse productivity with efficiency, which means producing finished goods at the lowest possible cost by optimizing the use of materials, time, and labor. While efficiency is another important measure, it provides managers with a different path to optimize resources for products.
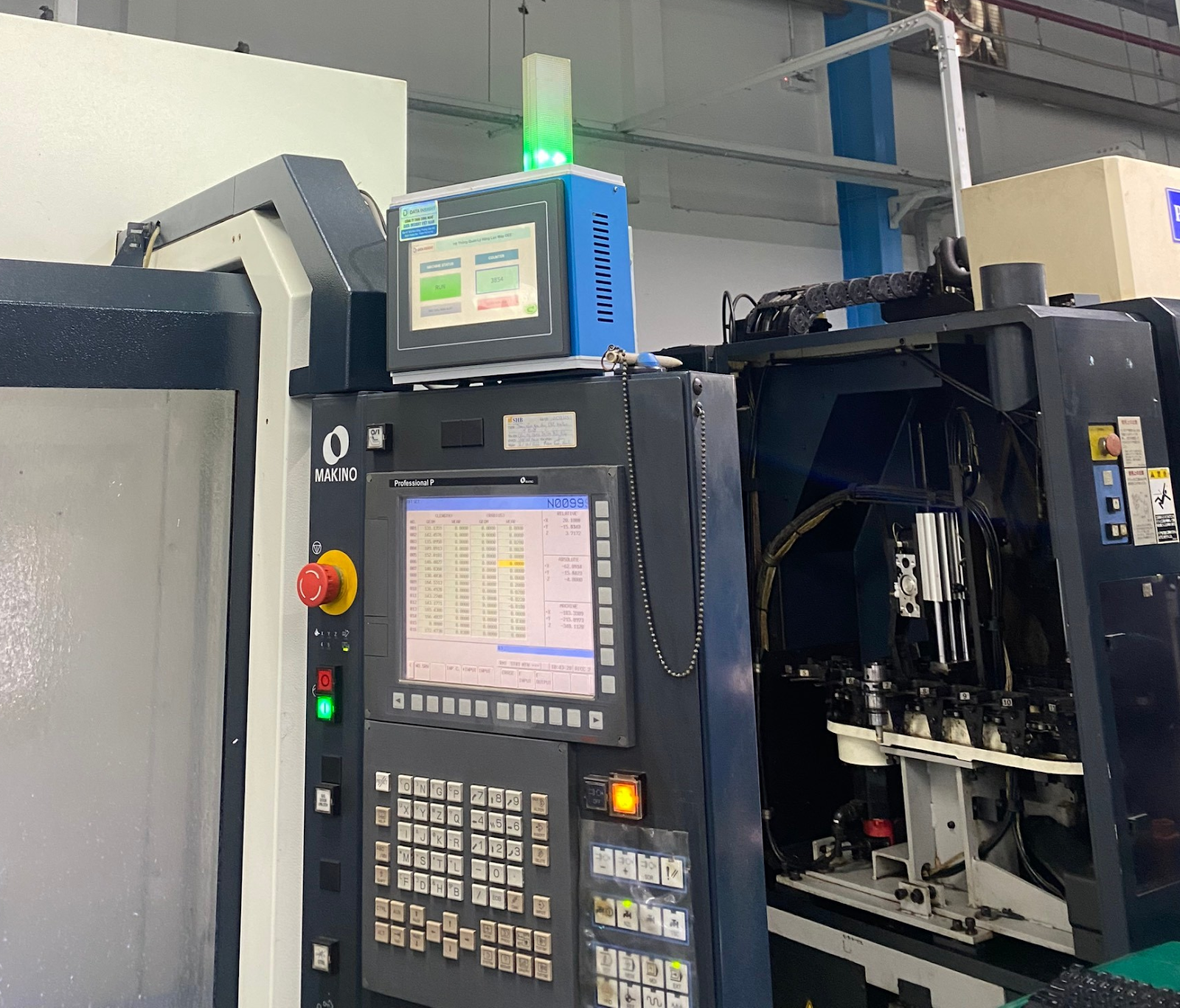
Formula for Calculating Machine Productivity
Machine productivity is a simple calculation involving the total number of products produced divided by the total hours the machine was used.
The measurement includes:
- Number of machines.
- Time period considered (shift, daily, or weekly hours).
- Accurate count of finished products or goods.
Using these variables, we have the formula for machine productivity:
Machine Productivity = Total number of products produced / Total machine hours
With machine data collection solutions like Data Insight, productivity can be monitored down to individual production lines, machines, or as part of a machine group.
A basic method of calculating machine productivity may be used for manual tracking prone to errors and legacy software systems where data needs adjustment. This basic measurement is a simple calculation of output versus input. Due to manual tracking or data residing in separate systems requiring transfer and adjustment, this method is limited by time and risk of data entry errors.
Using Overall Equipment Effectiveness (OEE) is a superior method for monitoring machine productivity. In an automated machine data platform, OEE tracks output and input more accurately than basic calculations allow. Employing OEE in machine productivity monitoring means machine speed and spindle, quality, tool wear, and various other variables are monitored in real-time.
By combining performance (speed), quality (total good parts), and time (standard operating time versus actual operating time), managers can see machine productivity at various levels—from the system level down to machines and plants—to make better decisions and optimize improvement efforts.
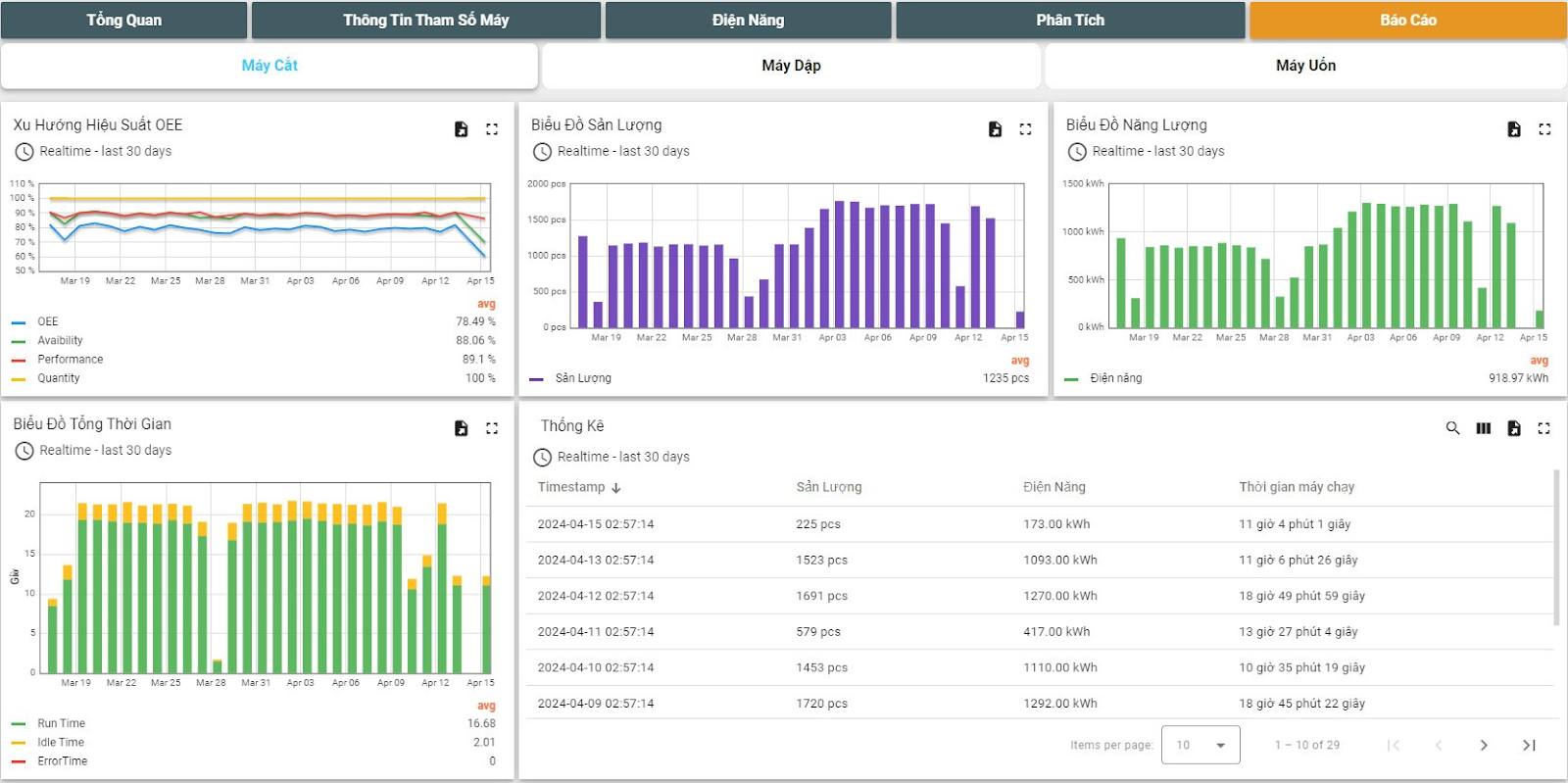
Benefits of Measuring Machine Productivity
By measuring production productivity, a company can better assess its manufacturing efficiency and plan more effectively for future production needs.
The benefits of measuring equipment productivity include:
1. Identifying staff deficiencies or training needs => Maximizing employee performance.
2. Comparing current output with set targets => Determining if goals are being met as planned.
3. Identifying areas for improvement and optimization.
4. Validating whether current processes are optimized or highlighting processes that need improvement in the future.
Another perspective that manufacturers can consider to monitor effectiveness is analyzing the performance of their machine operators.
The Importance of Automated Data Collection
Improving machine productivity can be achieved by using traditional systems that are divided or manually tracked. The challenge you will face is delayed, inaccurate, and impractical data. You will have to collect and aggregate reports manually, making it difficult to identify areas for improvement.
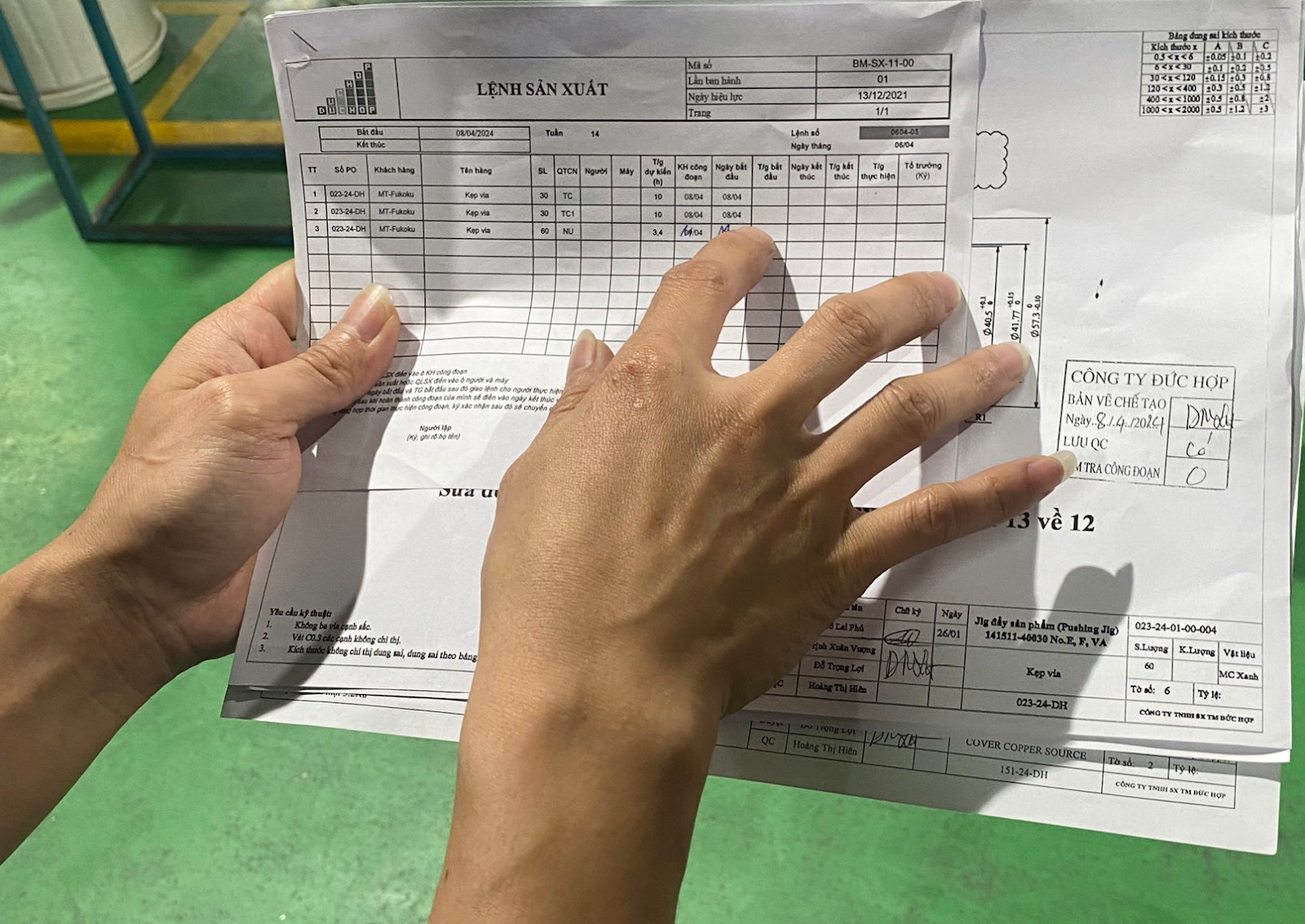
What would happen if all manual data collection and analysis could be automated?
Don’t worry because we – Data Insight – are on a mission for you; your machine data will be supported by our devices for gathering and utilized to enhance machine productivity across multiple areas on the factory floor. This eliminates the bottleneck of manual data collection, enabling humans and systems to take action based on the provided data.
Automated machine productivity measurements based on OEE can help businesses see where they are weak, whether there is any waste in production, and identify areas for improvement.
- Increased Accuracy and Reliability: Automated data collection and processing reduce reliance on human factors, minimizing errors due to incorrect or missing inputs. This leads to higher accuracy and reliability of analytical information.
- Time and Effort Savings: Automating the data collection and analysis process eliminates the need for manual intervention, saving time and effort for employees. Automated tasks can operate continuously and more quickly compared to manual tasks.
- Early Issue Detection and Improvement: Automated data allows for early detection of issues or improvement opportunities in the production process. Automated systems often have the capability to alert and provide real-time reporting on fluctuations or incidents in production.
- Optimization of Operations: Automating data collection and analysis helps optimize overall production operations. By automatically processing data and providing detailed information on performance and production capabilities, managers can make smarter and more effective decisions.
- Enhanced Strategic Direction: Having automated data and quick reports enables businesses to seamlessly and effectively monitor and evaluate their production strategies, allowing for real-time adjustments and improvements to business plans.
Optimizing Your Equipment Productivity
Many businesses invest heavily in equipment for their factories without always knowing how to optimize the operation of these machines most effectively. The reason optimization may not have been achieved could be due to inadequate management or a lack of measurement of machine performance.
The first thing we want to emphasize is the need for equipment to support data collection from your devices. This will show you which areas of machines are performing well and which areas have room for improvement. Below are some suggested ideas for optimizing equipment productivity, but first, let’s get started with collecting data from your machines.
Operator Training
Modern manufacturing machinery is complex and often equipped with IoT capabilities or at least basic automation. Providing precise operating instructions for employees and utilizing standard operating procedures will lead to more stable machine operations.
Process Review
A process map helps review the entire product workflow and establishes a culture of process improvement. When technology is deployed throughout the factory, workflows can be adjusted to leverage new capabilities and uncover areas for improvement.
Develop Condition-based or Predictive Maintenance Strategies
Condition-based maintenance used to be a decisive factor in reactive maintenance programs of the past. However, deep understanding and effective utilization of how products run on machines—and the significance of run cycles for necessary maintenance—are entirely possible now. Instead of costly and time-consuming periodic maintenance, consider using machine conditions to drive maintenance activities.
Focus on Equipment Utilization
Many companies often overlook the utilization of their equipment. As a result, improving productivity becomes challenging. A machine utilization strategy based on OEE (Overall Equipment Effectiveness) will unlock capacities and increase output without changing inputs.
Enhance Communication
In many traditional data monitoring systems, data is fragmented and poorly communicated. Machine productivity can be optimized by improving communication between humans and machines. Automatic data monitoring combined with alerts and notifications facilitates smooth, purposeful, and accurate communication.
Unlocking Data and Automation
Optimizing a manual data monitoring system is no small challenge. Data is often delayed and prone to errors, resulting in incomplete and inaccurate information.
The best way to optimize machine productivity is by using a machine connectivity solution. With access to accurate production data directly from machine controls, machines can transition to OEE-based productivity measurements that identify bottlenecks, defects, and trends in real-time.
As machine uptime and quality improve, production output increases significantly. This increase is directly related to unlocking “hidden capacity” that allows machines to produce more due to better resource and input management.
Data Insight provides automated production monitoring through real-time data collection from devices and sensors. The platform delivers valuable real-time insights that enable your company to optimize equipment productivity and manage inputs accurately to achieve substantial output increases.
If you’re interested in how Data Insight provide you our software to improve efficiency of your plant and drive profit for your business, don’t hesitate to schedule a demo with our team.
Contact us now at!
DATA INSIGHT TECHNOLOGY VIETNAM COMPANY LIMITED
- Hotline: 0916.848.638
- Hanoi office: Số 6 Kim Đồng, phường Giáp Bát, Quận Hoàng Mai, Thành phố Hà Nội, Việt Nam
- HCM City office: 99 đường Cộng Hòa, Phường 4, Tân Bình, Thành phố Hồ Chí Minh, Việt Nam