Việc quan tâm đến các chiến lược Lean có thể mang lại lợi ích cho quy trình sản xuất của bạn được như thế nào? Với nhiều chiến lược Lean tuyệt vời, làm thế nào để bạn có thể tìm ra phương pháp nào sẽ có ảnh hưởng lớn nhất đến doanh nghiệp của mình?
Một phương pháp hay đó là xem xét các kỹ thuật Lean hiện đang cho thấy hiệu quả của chúng ở nơi quan trọng nhất – trên phân xưởng sản xuất. Dưới đây, chúng tôi chia sẻ một mô tả ngắn gọn về 5 chiến lược Lean hiệu quả cùng với giải thích về cách mỗi công cụ có thể cải thiện quy trình sản xuất của bạn. Hãy ghi nhớ rằng, mặc dù sản xuất tinh gọn và các kỹ thuật Lean cụ thể có thể có tác động đáng kể đến doanh nghiệp của bạn theo từng phần, bạn còn có thể nhân lên lợi ích bằng cách kết hợp chúng.
Kaizen (Cải tiến liên tục)
Kaizen là một triết lý và phương pháp quản lý của Nhật Bản tập trung vào cải tiến liên tục trong mọi khía cạnh của doanh nghiệp. Từ “Kaizen” có nghĩa là “cải tiến” (kai) và “tốt” (zen). Triết lý này khuyến khích mọi nhân viên, từ quản lý đến công nhân, đóng góp ý kiến và thực hiện những thay đổi nhỏ nhưng liên tục để nâng cao hiệu quả và chất lượng công việc. Kaizen được áp dụng rộng rãi trong sản xuất, dịch vụ và nhiều lĩnh vực khác nhằm tăng cường năng suất và sự hài lòng của khách hàng.
5S (Hệ thống 5S)
Phương pháp 5S nhấn mạnh vào việc tổ chức khu vực làm việc của bạn. Chiến lược này bao gồm:
- SÀNG LỌC: Loại bỏ những thứ không cần thiết.
- SẮP XẾP: Sau khi hoàn thành sàng lọc, các vật dụng còn lại sẽ được sắp xếp ngăn nắp.
- SẠCH SẼ: Tạo ra một khu vực làm việc sạch sẽ.
- TIÊU CHUẨN HÓA: Viết ra các tiêu chuẩn cho từng yếu tố của quy trình trên.
- DUY TRÌ: Áp dụng thường xuyên các tiêu chuẩn để duy trì sự sạch sẽ và ngăn nắp.
Mục tiêu của 5S là loại bỏ lãng phí, cải thiện hiệu quả làm việc, tăng cường an toàn, và tạo ra một môi trường làm việc dễ chịu, giúp nâng cao năng suất và chất lượng sản phẩm. Phương pháp này không chỉ được áp dụng trong các nhà máy sản xuất mà còn trong các văn phòng, bệnh viện và nhiều loại hình tổ chức khác.
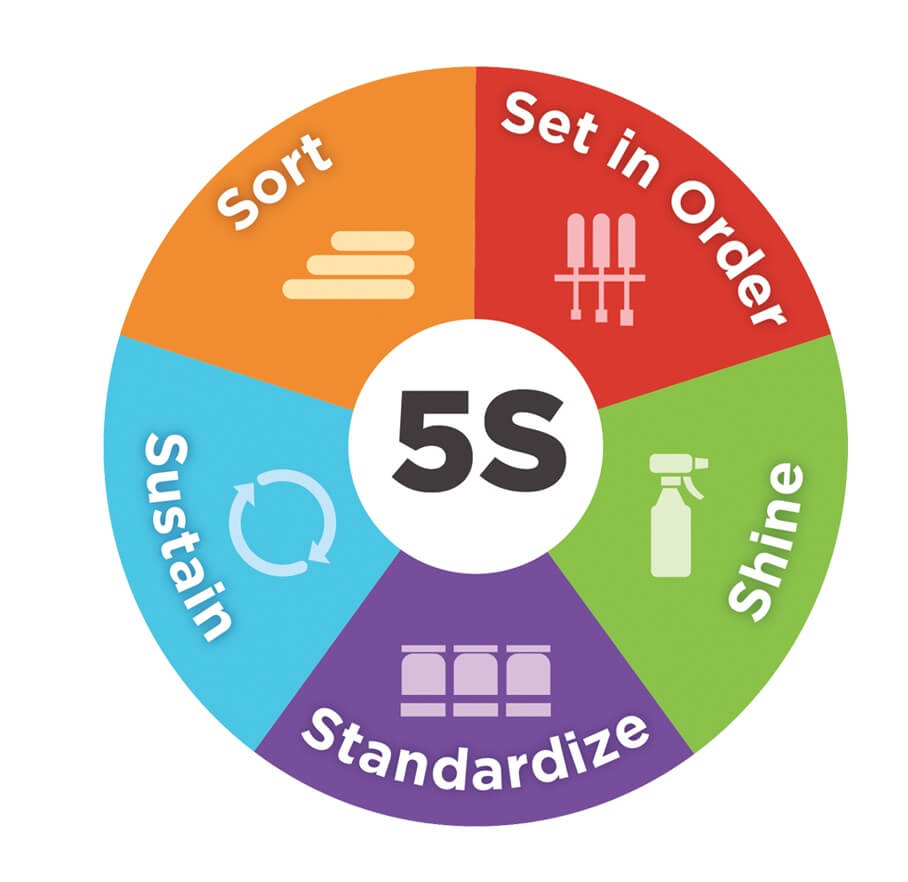
Sáu tổn thất lớn
6 tổn thất lớn (Six Big Losses) là một khái niệm trong quản lý sản xuất và bảo trì, tập trung vào việc xác định và loại bỏ các nguyên nhân chính gây lãng phí trong quy trình sản xuất. Các tổn thất này ảnh hưởng trực tiếp đến Hiệu suất tổng thể của thiết bị (OEE – Overall Equipment Effectiveness) và bao gồm:
- Hư hỏng thiết bị: Thời gian ngừng máy do sự cố kỹ thuật hoặc hỏng hóc thiết bị. Đây là tổn thất lớn nhất và có thể gây gián đoạn nghiêm trọng cho quy trình sản xuất.
- Điều chỉnh và thiết lập: Thời gian ngừng máy khi thay đổi công cụ, thiết lập thiết bị mới hoặc điều chỉnh để sản xuất một sản phẩm khác.
- Hoạt động tạm ngừng: Các dừng tạm thời hoặc hoạt động không liên tục do các sự cố nhỏ, thiếu nguyên liệu, hoặc vấn đề nhỏ với thiết bị. Đây là những tổn thất không quá lớn nhưng xảy ra thường xuyên.
- Tốc độ sản xuất chậm: Thiết bị hoạt động dưới tốc độ thiết kế hoặc tốc độ tối ưu. Nguyên nhân có thể do vấn đề kỹ thuật, mài mòn thiết bị, hoặc không tuân thủ quy trình vận hành.
- Sản phẩm lỗi: Sản phẩm bị hỏng hoặc không đạt chất lượng trong quá trình sản xuất hoặc trong giai đoạn khởi động hoặc thiết lập ban đầu, thường xảy ra khi bắt đầu một ca sản xuất mới hoặc sau khi thay đổi thiết lập, dẫn đến lãng phí nguyên vật liệu và thời gian.
Mục tiêu của việc xác định và giải quyết 6 tổn thất lớn này là cải thiện hiệu suất tổng thể của thiết bị, tăng năng suất, giảm lãng phí và tối ưu hóa quy trình sản xuất. Bằng cách tập trung vào các tổn thất này, doanh nghiệp có thể nâng cao chất lượng sản phẩm và hiệu quả hoạt động, góp phần vào sự phát triển bền vững và cạnh tranh trong thị trường.
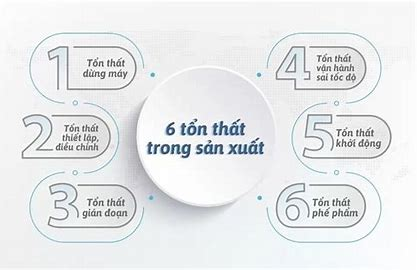
Hiệu Suất Thiết Bị Tổng Thể (OEE)
OEE cung cấp một tiêu chuẩn để đo lường hiệu suất trong một quy trình sản xuất cụ thể. Ba chỉ số được theo dõi bao gồm: Tính sẵn sàng, Hiệu suất và Chất lượng. Kỹ thuật Lean này tính toán và cung cấp cho bạn một phương pháp để theo dõi tiến trình trong việc loại bỏ lãng phí từ quy trình sản xuất. Đạt được 85% OEE là một mục tiêu lí tưởng của nhà máy. Khi đạt được mục tiêu này, bạn có thể tập trung vào các phương thức bổ sung để nâng cao kết quả của mình.
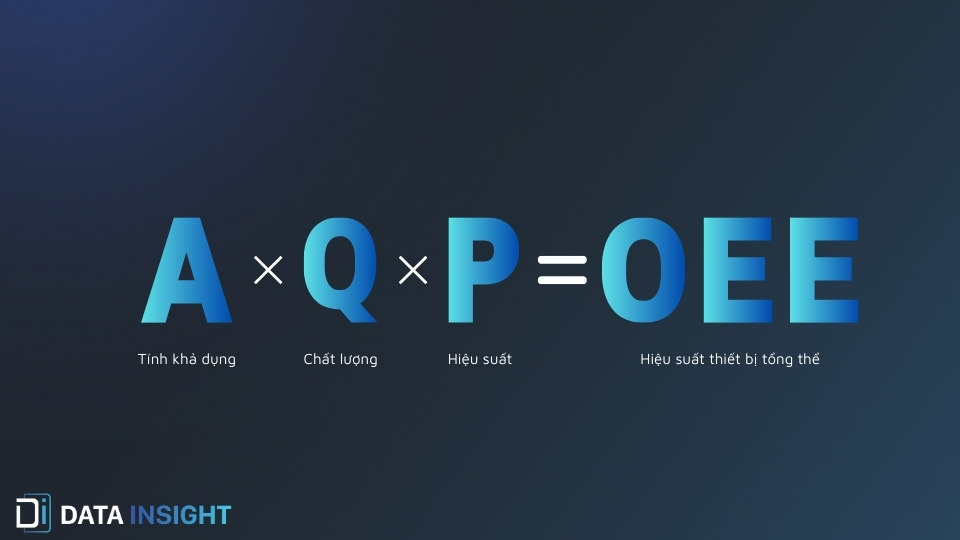
Giám Sát Máy Móc
Giám sát máy móc kết hợp hoàn hảo với OEE. Phần mềm giám sát máy móc tự động thu thập dữ liệu từ các máy và sử dụng dữ liệu này để cung cấp hình ảnh và thông báo theo thời gian thực, cũng như phân tích lịch sử để giúp các nhà vận hành và quản lý đưa ra quyết định nhanh hơn và chính xác hơn. Ngoài việc cung cấp cho bạn cái nhìn chi tiết về hiệu suất trên từng máy, giám sát máy móc còn mang đến cho bạn cái nhìn toàn diện về toàn bộ quy trình sản xuất của mình. Nếu bạn sử dụng phần mềm quản lý sản xuất dựa trên đám mây bảo mật, nó cũng sẽ đưa thông tin vào tầm tay bạn ở bất cứ đâu có kết nối Internet.
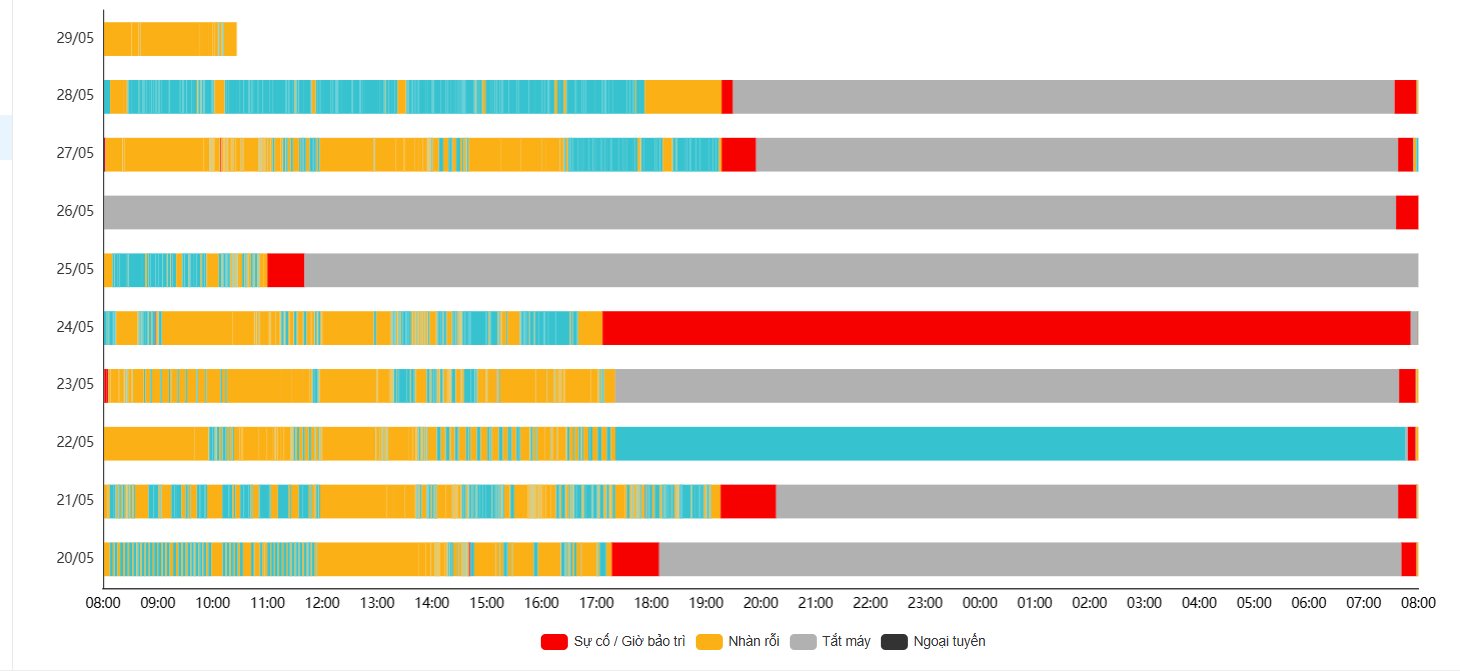
Thời gian ngừng máy, vấn đề về chất lượng, và hiệu suất kém có thể được phân tích tự động hoặc bởi nhà quản lý. Bạn có thể thấy qua thử nghiệm rằng sự kết hợp các kỹ thuật Lean mang lại kết quả tối ưu. MES-Lite có thể đóng vai trò là nền tảng cho bất kỳ chương trình sản xuất tinh gọn nào bằng cách cung cấp phân tích sản xuất theo thời gian thực và cho phép bạn theo dõi tác động tích cực mà các triển khai Lean của bạn có lên năng suất và hiệu quả theo thời gian.
Mọi thông tin xin vui lòng liên hệ:
Công ty TNHH Công Nghệ Data Insight Việt Nam
- Hotline: 0916.848.638
- VP Hà Nội: Số 6 Kim Đồng, phường Giáp Bát, Quận Hoàng Mai, Thành phố Hà Nội, Việt Nam
- VP Hồ Chí Minh: 99 đường Cộng Hòa, Phường 4, Tân Bình, Thành phố Hồ Chí Minh, Việt Nam.