Sản xuất tinh gọn là gì?
Sản xuất tinh gọn là một phương pháp được thành lập từ sự tiếp cận chiến lược vào cải thiện không ngừng và bền vững qua sự loại bỏ hoàn toàn các lãng phí và các yếu tố kém hiệu quả xuyên suốt doanh nghiệp.
Sản xuất tinh gọn không chỉ là sự tuân theo những bộ quy tắc, mà nó là một sự tiếp cận mang tính triết lý, đòi hỏi phải thay đổi cách nhìn nhận, tư duy phổ biến trong tổ chức để tiến tới một sự đổi mới, học hỏi và linh hoạt. Một bộ tập hợp những lý tưởng của triết lý này có thể kể đến là Hệ thống sản xuất Toyota (Toyota Production System – TPS), một tập hợp những nguyên tắc có sự ảnh hưởng tới nhiều tổ chức “tinh gọn” hiện nay. Một số khái niệm, tên gọi là bạn có thể thấy trong một tổ chức “tinh gọn” là:
- Đo lường tất cả mọi thước đo, KPIs
- Trực quan hóa dữ liệu
- Thành lập dòng chảy giá trị
- Hướng tiếp cận sản xuất theo nhu cầu
- Chiến lược “Kéo” sản phẩm theo nhu cầu
Sự tóm lược ngắn gọn về lịch sử của Sản xuất tinh gọn
Sự phát triển của Sản xuất tinh gọn có thể được truy vết lại qua toàn bộ lịch sử, ngay cả trước khi sự ra đời của Hệ thống sản xuất Toyota. Khi khát vọng của con người để cải thiện các hệ thống để trở nên hiệu quả hơn, Frederick Taylor viết lên những ý tưởng ban đầu và sản xuất tinh gọn (cho dù không cái tên chưa được biết tới), phát hành ra cuốn The Principles of Scientific Management (tạm dịch: Các nguyên tắc về quản lý một cách khoa học) năm 1911. Henry Ford thường được nhắc tới là điểm xuất phát thực sử của “Tinh gọn”, ảnh hướng tới cả những nguyên tắc của Toyota sau này, bởi sự chán ghét dành cho các lãnh phí đã dẫn tới ông cắt giảm một cách mạnh mẽ mọi sự “kém hiệu quả” ở doanh nghiệp sản xuất xe của ông.
Học hỏi các phương pháp từ những tài liệu sơ khai này, Taiichi Ohno bắt đầu phát triển quy trình sản xuất xuất chúng của Toyota và, với họ, Hệ thống sản xuất TPS. John Krafcik, một cựu sinh viên trường MIT giờ đây đang làm việc ở Hyundai, là người chính thức tạo ra thuật ngữ “Tinh gọn” thông qua một bài nghiên cứu được phát hành vào cuối những năm 1980 hoạch định ra rằng các cơ sở sản xuất nên bám theo những kiểu dạng quy tắc này để có thể vận hành tốt hơn cả về năng suất và chất lượng, và cả cách để các doanh nghiệp có thể suy giảm các rủi ro sản xuất khi áp dụng phương pháp “Tinh gọn” này.
Năm nguyên tắc của Sản xuất tinh gọn
Điểm bắt đầu của mọi tổ chức khi bắt đầu chiến lược “Sản xuất tinh gọn” là bắt đầu với chiến lược 5S, một bộ nguyên tắc dẫn dắt công ty hướng tới một lượng sản phẩm sản xuất tổ chức hơn, hiệu quả hơn và gọn gàng hơn, đặt ra nền tảng cho những chiến lược tinh gọn phức tạp hơn và chuyên sâu hơn. Và mỗi chữ “S” trong 5S sẽ đại diện cho:
- Sàng lọc (Sort): Sàng lọc và phân biệt ra những thứ nào cần thiết và hay được sử dụng ra những thứ nào ít khi hay không bao giờ được sử dụng.
- Sắp xếp (Set in order): Tất cả mọi vật luôn được sắp xếp ở một vị trí cố định mà công nhân có thể sử dụng và cất đi. Các vật dụng này luôn phải được sắp xếp theo cách để tiện lợi cho công nhân dễ nhận thấy, phân biệt, lấy đi.
- Sạch sẽ (Shine): Thường xuyên vệ sinh, dọn dẹp mọi thứ tại nơi làm việc. Tạo ra một môi trường sạch sẽ và hạn chế các rủi ro do bụi bẩn gây ra
- Săn sóc (Standardize): Chuẩn hóa các công việc từ 3S ban đầu và biến nó thành một phương pháp tiêu chuẩn để vận hành và đánh giá chiến lược 5S được đặt ra cho nhà máy
- Sẵn sàng (Sustain): Duy trì, biến toàn bộ các công việc từ chiến lược 5S thành “thói quen” giúp cho toàn bộ nhà máy luôn trong tâm thế sẵn sàng làm việc
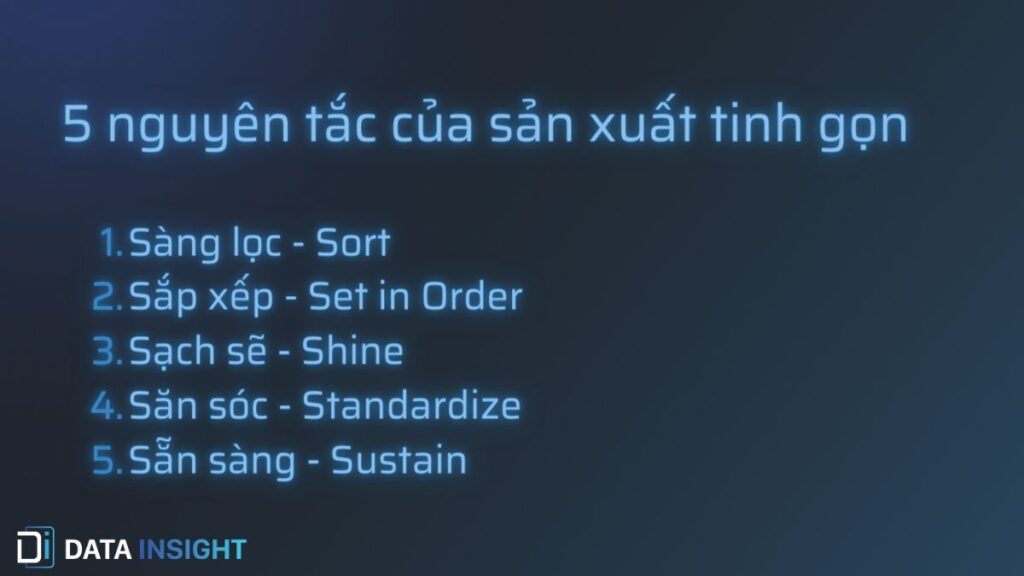
8 lãng phí trong Sản xuất tinh gọn
Loại bỏ các lãng phí trong quá trình sản xuất (cho dù là thời gian, tài nguyên, nhân lực) là một công việc quan trọng, ưu tiên lớn trong một chiến lược sản xuất tinh gọn. Trong đó, tồn tại 8 loại chuẩn hóa đã được định nghĩa, chuẩn hóa mà các nhà sản xuất có thể kiểm tra để có được một cái nhìn hoàn chỉnh hơn việc tổ chức đang mất lợi nhuận bởi những thứ thiếu hiệu quả nào.
- Khiếm khuyết: Khi có một thứ nào đó không vận hành chuẩn, khi đó sẽ có lãng phí và sẽ có sự suy giảm lợi nhuận. Sản phẩm kém chất lượng, bảo trì máy móc kém, sự thiếu chính xác ở mức độ tồn kho và đến cả sự thiết sót các tài liệu liên quan đều được xác định là khiếm khuyết
- Quy trình thừa thãi: Điều này xảy ra khi quy trình sản xuất diễn ra quá chậm hoặc quá phức tạp để có thể trở nên hiệu quả,.. Nó là một sự cản trở tới sản xuất hơn là cần thiết. Có thể bao gồm: Quy trình đóng dấu, báo cáo không cần thiết, dữ liệu giống nhau,..vv,..
- Sản xuất thừa: Quá nhiều sản phẩm và không đủ nhu cầu ở hiện tại dẫn đến thừa sản phẩm. Khi mà nhu cầu khách hàng trở nên không rõ ràng hoặc dữ liệu dự đoán không chính xác, thì sản xuất thừa có thể dẫn đến lãng phí trong thời gian, tài nguyên và nhân lực.
- Thời gian chờ: Có rất nhiều lý do khiến nhân viên có thể phải chờ đợi như là thời gian ngừng máy không kế hoạch, giao tiếp giữa các quy trình còn kém hay là thời gian chuẩn bị thiết bị cao. Nó là một sự lãng phí về mặt thời gian mà nhà máy sẽ hoàn toàn có thể cải thiện được
- Tồn kho: Hàng tồn kho an toàn là một trong những nơi mà các nhà sản xuất có thể gặp phải rắc rối với loại lãng phí này. Dự báo không chính xác, sản xuất thừa, hoặc giao kém tiếp giữa phòng ban sản xuất và mua hàng đều có thể dẫn tới lãng phí tồn kho
- Vận chuyển: Nếu tất cả mọi thứ cần thiết tồn tại những khoảng cách lớn để di chuyển giữa chúng thì nhà máy sẽ có rất lãng phí so với một không gian đã được tối ưu hóa một cách logic về quản đường di chuyển giữa chúng. Một sự lãng phí về vận chuyển có thể gây ra bởi bố trí nhà xưởng có thể là nguyên nhân dẫn tới nhiều lãng phí khác, ví dụ như lãng phí về thời gian chờ
- Chuyển động: Nếu một chuyển động xảy mà nó thực sự không cần thiết thì đó là lãng phí. “Chuyển động lãng phí” ở đây có thể nhắc tới dữ liệu, nguyên liệu thô, con người – hay bất cứ thứ gì đi nữa. Chuyển động lãng phí có thể bắt nguồn từ việc với, ngồi, ưỡn người cho đến cả vận hành tách biệt và lên kế hoạch sản xuất yếu kém.
- Nhân lực không được tận dụng: Nếu nhân viên được đào tạo yếu kém, đó sẽ là một lãng phí. Năng lực của nhân viên có thể bị tận dụng yếu kém do quản lý hay giao tiếp yếu kém hay là sự thất bại trong việc lôi kéo nhân viên vào việc thiết kế và phát triển công việc
Lợi ích của Sản xuất tinh gọn
Sản xuất tinh gọn đã trở nên vô cùng phổ biến đơn giản bởi vì: nó hiệu quả. Nói một cách chi tiết hơn, nó vận hành để làm giảm chi phí tồn kho chung, thời gian tăng ca, trì hoãn đầu tư gia tăng, gia tăng sản xuất và suy giảm thời gian sản xuất với trung bình 99%. Sản xuất tinh gọn cũng thể dẫn tới sự cải thiện trong dịch vụ khách hàng, chất lượng tốt hơn, cải tiến mạnh mẽ hơn, cải thiện vòng quay hàng tồn kho và thúc đẩy một cách rõ ràng năng suất và giá trị gia tăng trên mỗi người. Điều này mang lại được nhiều lợi ích tài chính và hỗ trợ công ty có thể mở rộng phạm vi hoạt động của họ. Chiến lược Tinh gọn cũng có thể thúc đẩy sự linh hoạt và khả năng cạnh tranh của doanh nghiệp.
Các lợi ích của Sản xuất tinh gọn:
- Cải thiện vòng quay hàng tồn kho
- Cải thiện Dịch vụ khách hàng
- Giảm lãng phí
- Cải thiện Mức độ thỏa mãn khách hàng
- Cải thiện Năng suất
- Cải thiện Thời gian sản xuất
- Cải thiện Chất lượng
- Thúc đẩy đổi mới
- Gia tăng lợi nhuận
Các công cụ và kỹ thuật của Sản xuất tinh gọn
Để có thể đạt được hàng loạt những lợi ích này, tồn tại rất nhiều công cụ và kỹ thuật cho doanh nghiệp học hỏi và áp dụng hiệu quả, hay là một phần mềm sản xuất tinh gọn để cho phép tiếp cận nó. Có một số công cụ vật lý như thẻ tag, hay là bảng công cụ. Cũng có các hệ thống, công cụ và kỹ thuật cho sản xuất tinh gọn mà nó thiên hướng triết lý hơn như:
Just In Time
Phương pháp này khuyến khích chiến lược sản xuất “Đúng sản phẩm, với đúng số lượng, tại đúng nơi, vào đúng thời điểm cần thiết”. Điều này suy giảm được những lãng phí về tồn kho.
Gemba
Phương pháp này nhắm tới không gian làm việc mà ở các công việc mang lại giátrị được thực hiện như là công xưởng sản xuất. Nhà quản lý có thể thường xuyên trực tiếp đi xuống và có một cái nhìn rõ ràng về các quy trình và các vấn đề thường trực liên quan đế nó, phương pháp này trong Sản xuất tinh gọn còn được gọi là “Gemba – Nơi làm việc”
Sơ đồ chuỗi giá trị
Đây là một công cụ vô cùng quan trọng đối với sản xuất tinh gọn, nó liên quan đến một sự trình bày trực hóa, dòng chảy giá trị, tất cả mọi thứ trong doanh nghiệp mà đều tạo ra giá trị. Lãng phí và sự kém hiệu quả trở nên rõ ràng hơn nhiều sử dụng phương pháp này.
Kaizen
Đây là một phương pháp mà đề cập đến một triết lý hoặc phương pháp quản lý mà nhấn mạnh vào việc tạo ra những cải tiến liên tục và không ngừng, trong mọi khía cạnh của doanh nghiệp
Điểm nút thắt cổ chai
Luôn tồn tại những nơi khi mà sự kém hiệu quả kéo toàn bộ năng suất xuống một nhịp độ thấp hơn những sản phẩm khác bao quanh nó trong sơ đồ giá trị của nó. Sự suy giảm các yếu tố kém hiệu quả ở đây sẽ có sức ảnh hướng vô cùng lớn, bởi tất các các thành phần khác của sản xuất có thể hỗ trợ sự phát triển của nó khi quy trình này không còn là yếu tố cản trở nó. Đó là “những thứ níu giữ lại doanh nghiệp của bạn”.
Kanban
Đây là một hệ thống lập kế hoạch mà sẽ phân tách những công việc thành các thành phần như: Phải làm, Đang làm, Đã làm xong để giúp cho nhà sản xuất có thể tập trung và quản lý điều gì là cần thiết trong thời điểm đó.
Dòng chảy liên tục
Phương pháp này hướng tới duy trì dòng chảy sản xuất trong mọi thời điểm mà tồn tại ít hoặc không tồn tại lãng phí và thời gian ngừng sản xuất. Và dòng chảy liên tục này đòi hỏi năng lực của nhà sản xuất trong việc kiểm tra, đánh giá và cải thiện sản phẩm và quy trình sản xuất của nó.
Được trang bị với các công cụ trên và cộng thêm sự cởi mở với phương hướng hoạt động hoàn toàn mới bằng cách thực hiện những sự thay đổi có hệ thống, chuyên sâu, nhà sản xuất có thể tạo ra được các cơ sở và quy trình sản xuất được tối ưu hóa và loại bỏ hoàn toàn các lãng phí cũng như đẩy mạnh quy trình sản xuất và tiềm năng phát triển của doanh nghiệp thông qua Sản xuất tinh gọn.
Cảm thấy thú vị về nền tảng AIOT của Data Insight dành cho các nhà sản xuất có thể thúc đẩy sự cải tiến không ngừng như thế nào?
Đạt được sự tường minh trong thời gian thực về năng suất của công xưởng, theo dõi những thước đo đánh giá quan trọng nhất của bạn, suy giảm thời gian ngừng sản xuất và nhiều hơn nữa với giải pháp nền tảng AIOT của chúng tôi.
Mọi thông tin xin vui lòng liên hệ:
Công ty TNHH Công Nghệ Data Insight Việt Nam
- Hotline: 0916.848.638
- VP Hà Nội: Số 6 Kim Đồng, phường Giáp Bát, Quận Hoàng Mai, Thành phố Hà Nội, Việt Nam
- VP Hồ Chí Minh: 99 đường Cộng Hòa, Phường 4, Tân Bình, Thành phố Hồ Chí Minh, Việt Nam.